Optimizing Tooling Efficiency
In the realm of sheet metal fabrication, the efficiency of tooling systems plays a pivotal role in enhancing overall productivity. Utilizing advanced tooling solutions such as Pivatic quick tool change system, which is featured in all PivaPunch lines, can significantly streamline operations. Tools for different product families can be changed very efficiently to reduce downtime and enhance throughput. This capability is essential for manufacturers aiming to maintain flexibility in production without sacrificing speed or quality. PivaPunch can handle various material types and thicknesses, accommodating up to 6 mm thick steel strip also as pre-painted, plastic-covered, galvanized, or cold-rolled.
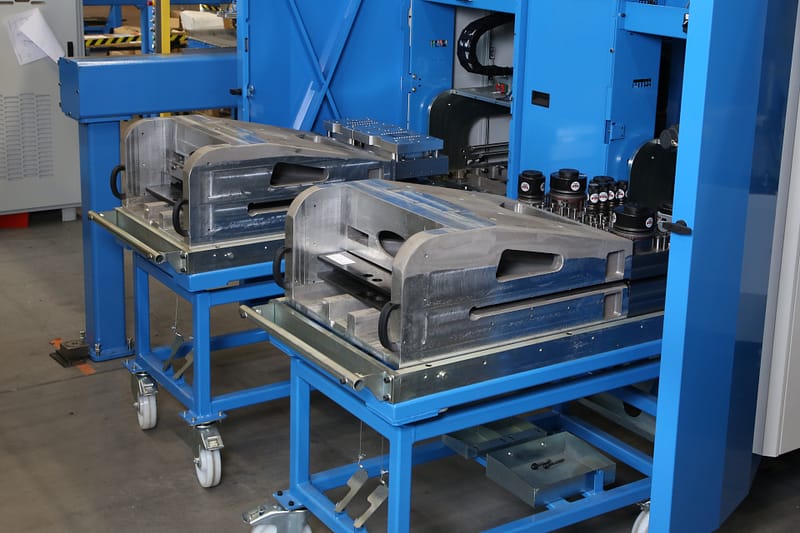
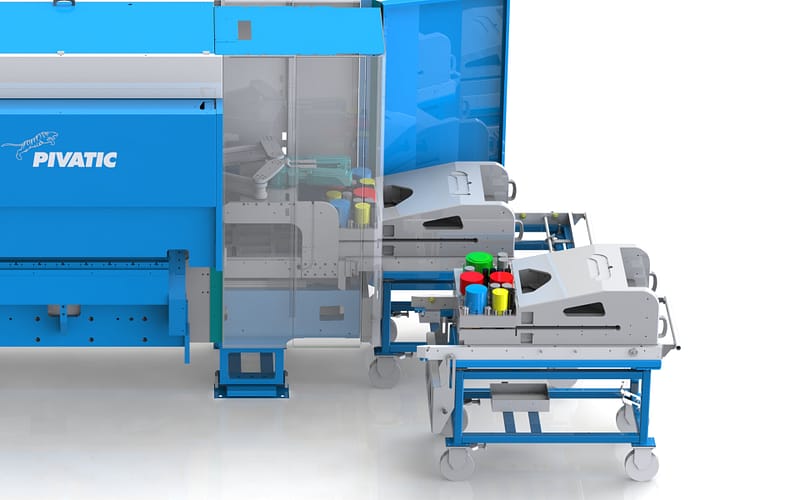
Moreover, the integration of dedicated press tools alongside Thick Turret tooling further amplifies capacity. This combination facilitates a broader range of punching patterns, perforations, and embossing, thereby expanding the capabilities of a single machine. The quick-change feature of both Thick Turret and press tools, often achievable in under a minute, exemplifies the kind of rapid adaptability needed in modern production environments to meet diverse client demands swiftly.
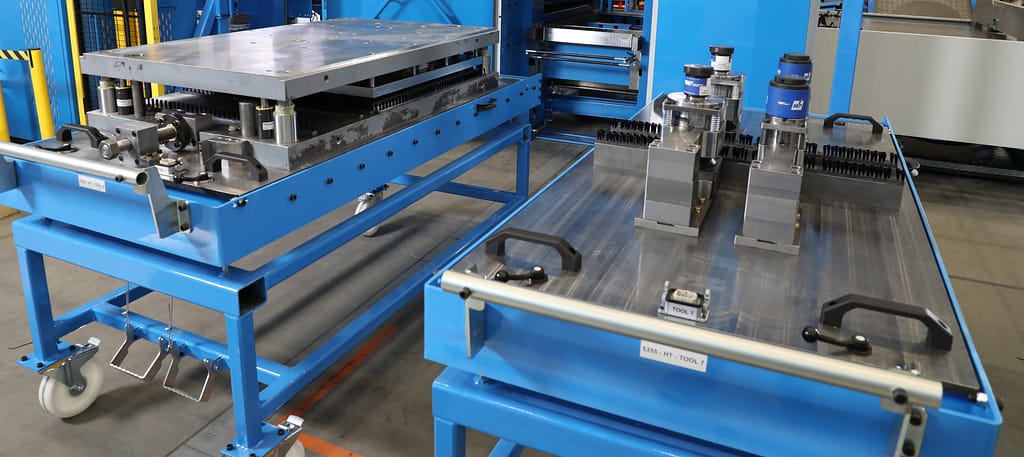
Advancements in Material Handling and Automation
The transition towards automated material handling systems marks a significant leap in productivity for sheet metal punching processes. PivaPunch systems exemplify this shift by eliminating the need for manual material handling, thereby reducing labor costs and minimizing human error. Automation ensures that materials are not only handled more efficiently but also with greater care, preserving the quality of sensitive materials like pre-painted or plastic-covered metals. This precise handling is crucial in maintaining the aesthetic and functional quality of the final products.
Enhancing Throughput with Double Tool Punch Technology
The Double Tool Punch technology in PivaPunch represents a significant innovation in the punching process compared to traditional methods. By allowing two punches to occur simultaneously, this technology effectively doubles the punching capacity of the machine. This is particularly beneficial in high-volume production settings where time is of the essence, and production speed directly correlates with profitability.
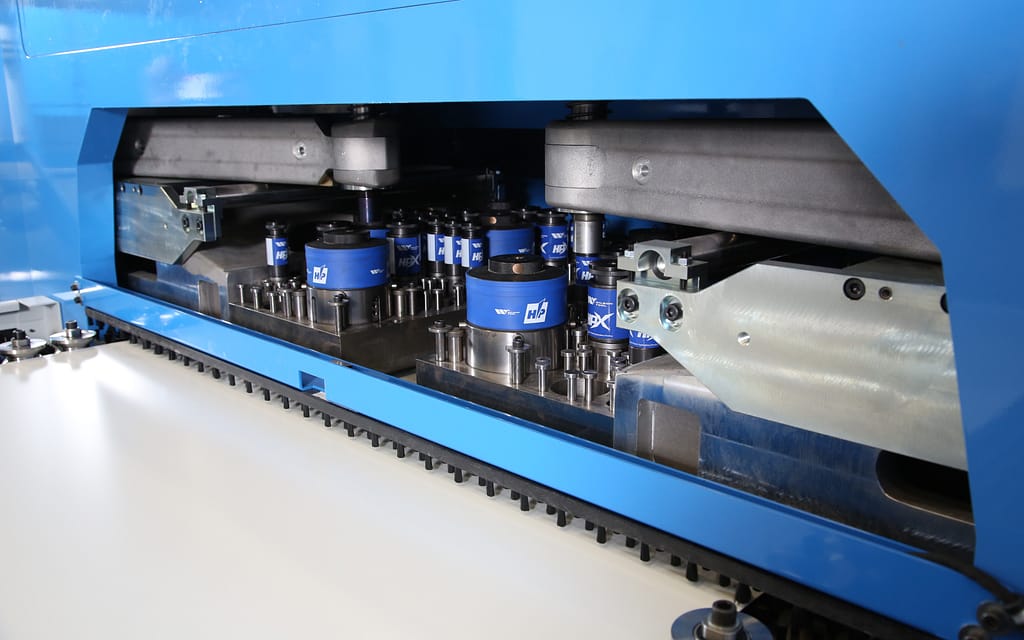
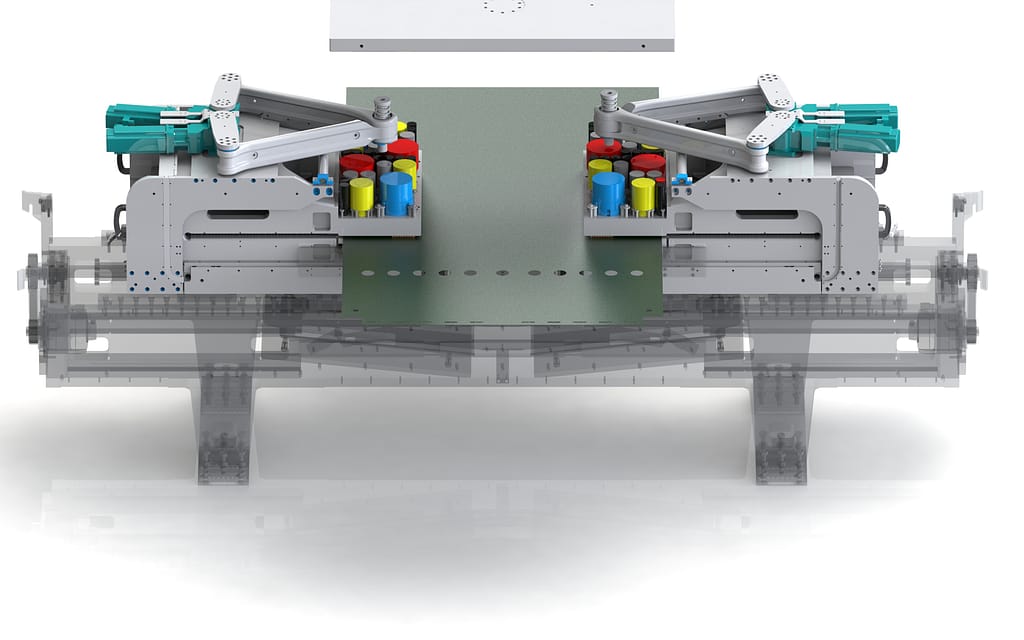
Furthermore, the precision of this technology ensures that each punch is executed with minimal burr, reducing the need for secondary finishing processes and thereby streamlining the production line. The reduced tool wear also contributes to longer maintenance intervals, thus lowering the overall maintenance costs and downtime associated with tool servicing.
Integrating Follow-up Processes for Streamlined Operations
The capability to integrate follow-up processes such as bending or roll forming directly after the punching stage saves time but also reduces the handling errors that can occur when moving parts between separate machines. Such integrations are particularly advantageous in the production of complex or large parts like steel doors or air handler casings, where multiple fabrication steps are typically required. By consolidating these steps into a cohesive, automated line, manufacturers can achieve significant gains in efficiency and consistency in output quality.
By focusing on these advanced techniques and technologies, manufacturers can significantly enhance the productivity and efficiency of their sheet metal punching operations. The continuous evolution of punching technology, coupled with strategic automation, sets the stage for meeting the increasing demands of the industry while maintaining high standards of quality and precision.