Economical Standpoint
For sheet metal manufacturing it is possible to buy raw standard coils or slitted coils from steel suppliers, or blanks from steel service centres, but in the end the starting point is always a sheet metal coil that is made from ore-based smelting or scrap-based smelting. This process produces carbon dioxide, and it is not possible to produce steel without forming carbon dioxide – which is why we should optimize our material usage from the beginning. With Pivatic coil punching you may utilize raw coils to boost your economic standpoint to maximize material usage, so that the very minimum amount of scrap will be produced in your factory and the steel suppliers’.
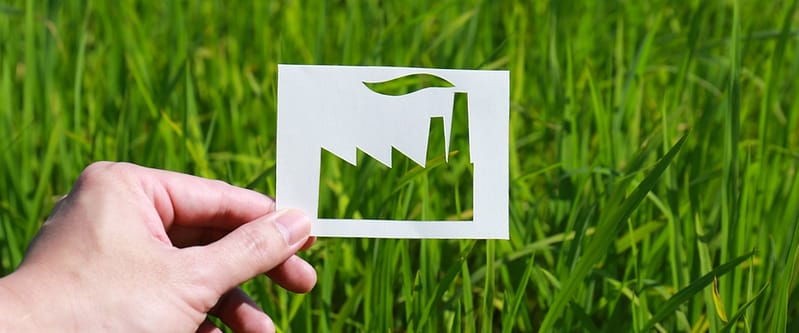
The main benefit of PivaPunch coil punching is the continuous coil strip. As the process is running there are very few changing factors, making the manufacturing of parts reliable. The parts are produced back-to-back from the coil with no time wasted on unloading or buffering. There is also no scrap in X-direction as parts are cut to the correct length from the coil. Very long parts can also be produced without additional investment or processing time.
Punching Lines for Coils
PivaPunch PCC (Punching Center for Coils) is a fully automated punching solution that is capable of unmanned production. It is capable of handling coils of 200 – 1830 mm (7.78” – 72”) in width, up to 25tn in weight.
Coil Handling
The PCC starts with a strip feed from a loaded coil. The decoiler system can be tailored to have loaded 1 – 3 coils simultaneously, and 1 – 4 coils in coil cars or coil storage system next to it. In a multi-decoiler system, the process can automatically change from one material to another in under 2 minutes. Changing a loaded coil to another from a storage can be done manually in under 3 minutes.
After decoiling, the strip is straightened and the coiling tensions are removed. The straightening rolls and drive motors are chosen according to the material thickness range specified. The straightener settings can be imported from readouts, parameters stored in the controller, and/or according to coil diameter. The strip is fed continuously to a buffer loop to prevent pressing marks.
Punching
The strip is fed to the TT Thick Turret punching station by a CNC-adjustable roll feeder or gripper feeder. The roll feeder is for thin and narrow coil materials, and it is mounted on a solid steel frame. Both upper and lower feeding rolls are driven by an AC servo motor with a precision gearbox and timing belt transmission. The gripper feeder is for thicker materials and has one or more hydraulic clamps set on a bridge element that moves the material in the X-direction. A clamp holds the material still on the return stroke of the gripper feeder. In both cases, the strip is guided with guiding elements on both the entry side and the exit side of a feeder bed.
The Turret Punching is done by tools set in two traversing tool cassettes, with the punching stroke done by a single ram plate. Punching, embossing, notching, thread forming, and piercing are standard features. For a higher efficiency in parts containing special features, or for better flexibility in variable part production, a HT Hard Tool press station or a LT Large Tool punching station can be included after the TT Thick Turret punching station.
Shearing and follow-up processes
When the punching process is finished for a part, it is sheared to the correct length from the coil by a hydraulic or electrical shear and conveyed to the follow-up process. If a press tool was used and there is curvature to the part, it can be fine straightened by a leveler. The part can be stacked or buffered automatically in the PivaPunch or fed to a process like bending or roll forming. It is possible to flip the part over prior to stacking or bending, to have the burr on top of the part (inside of the part when bent). Additional special equipment can be integrated into the line if required, such as a strip lubrication device, PVC film decoiler, inkjet printer, labeling device, or a strip recoiler.
Thick Turret, Large Tool and Hard Tool stations
Coil Nesting
When talking about coil nesting, the traditional way is perceived as suitable for mainly big parts as large batches back-to-back. Our nesting systems give you multiple options to run your parts. You may choose the part type, amount, and the order in which you want the parts to exit the system. All parts of the same material can be produced from one wide coil, nested side-by-side.
A back-to-back nested coil is done by traditional coil punching equipment. To nest parts side-by-side on a strip, Pivatic uses a CTW Cut-to-Width station to split the nested blank that is cut from the continuous strip. There is potentially no waste in the Y-direction by filling the coil width with nested parts. For high quality part production, the CTW can also act as an edge trimmer in prior to the punching in a PivaPunch PCB Punching Center for Blanks.
Thick Turret and Cut-to-Width stations
Production Methods for Coil Nesting
Pivatic has been producing coil punching machines since 1975 and have seen the trends change in part production. The batch sizes are getting smaller and the need for flexibility increases. Based on our current customers we have identified and adapted to three different production methods:
Batch production: The most efficient way is the batch production, where you run the weekly, monthly, or even yearly requirement of a single part in one go. The deciding factors are the cycle time and material optimization. Parts are usually stacked ready for storage. We choose the optimal coil width for nesting the required parts and split all parts from the nest with single shear strokes. You get the best possible edge quality in all part sizes.
Kit production to optimize material: When the batch sizes are smaller, are based on orders, or there is limited storage space, you might only need 10 or 100 parts at a time. To optimize material in this scenario, it is usually beneficial to produce 1-3 parts more or less since you are producing from a continuous strip instead of a standard sheet. The cost of the extra parts is usually compensated by the saved material.
Kit production in the correct order: When there is a follow-up process after PivaPunch, most commonly bending or assembly, it is possible to produce only the required number of parts and in the correct order. This means that batch size of one is possible. The material optimization lacks but you will not produce any unneeded parts or skeletons to complicate the process.