The megatrends transforming the construction industry is urbanization: more and more high apartments, commercial and office buildings, shopping centers and factories are being built. The buildings require several types of sheet metal products, such as panels for façade, ceiling and floor – doors for hotels and factories – and elevators for high hotel and office buildings. The building is always project-based and scheduled, and the aesthetics are important to have visually appealing looks.
The construction process has requirements for permits, architectural features, functionalities, implementation, environmental care and durability – which all affects the material choices.
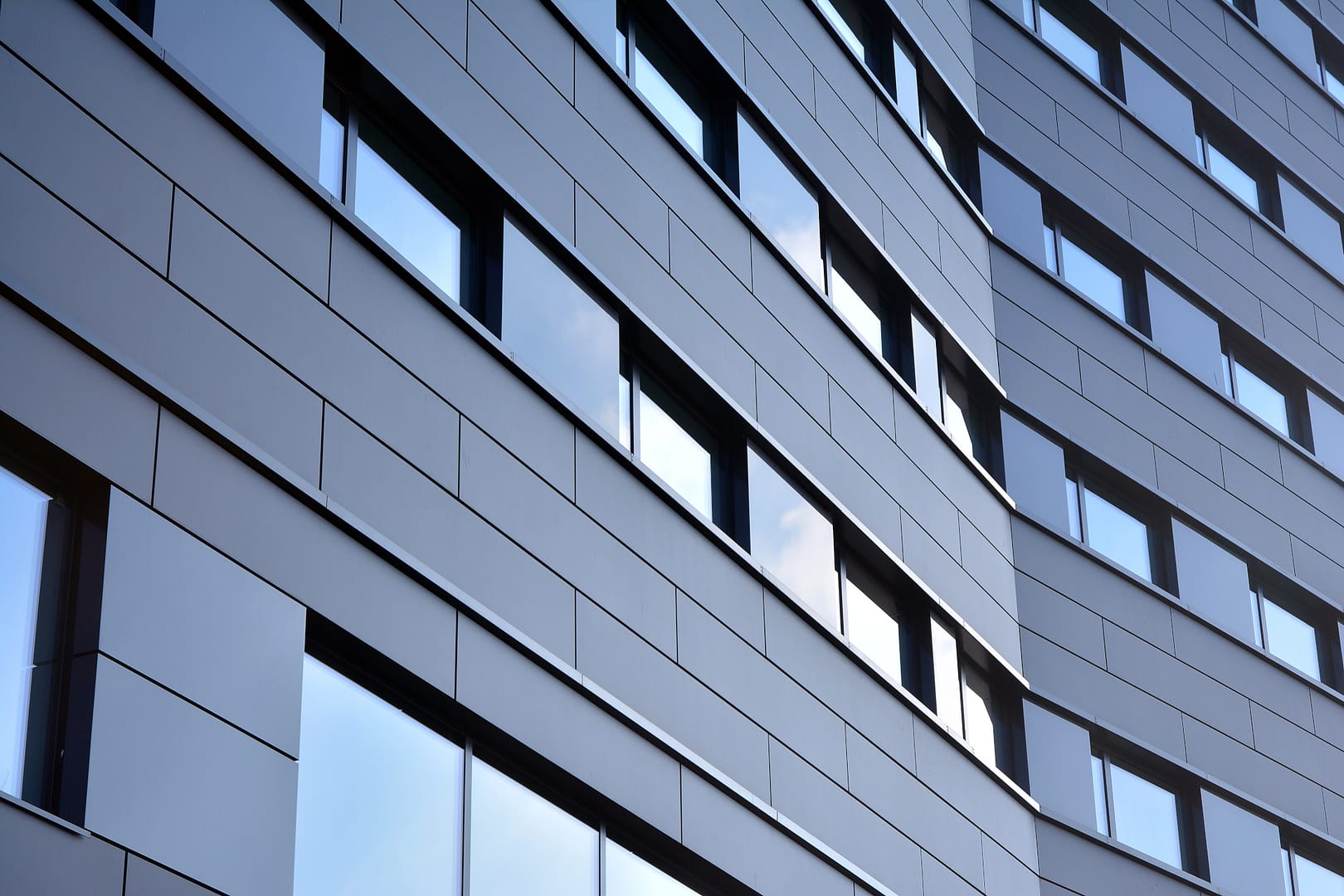
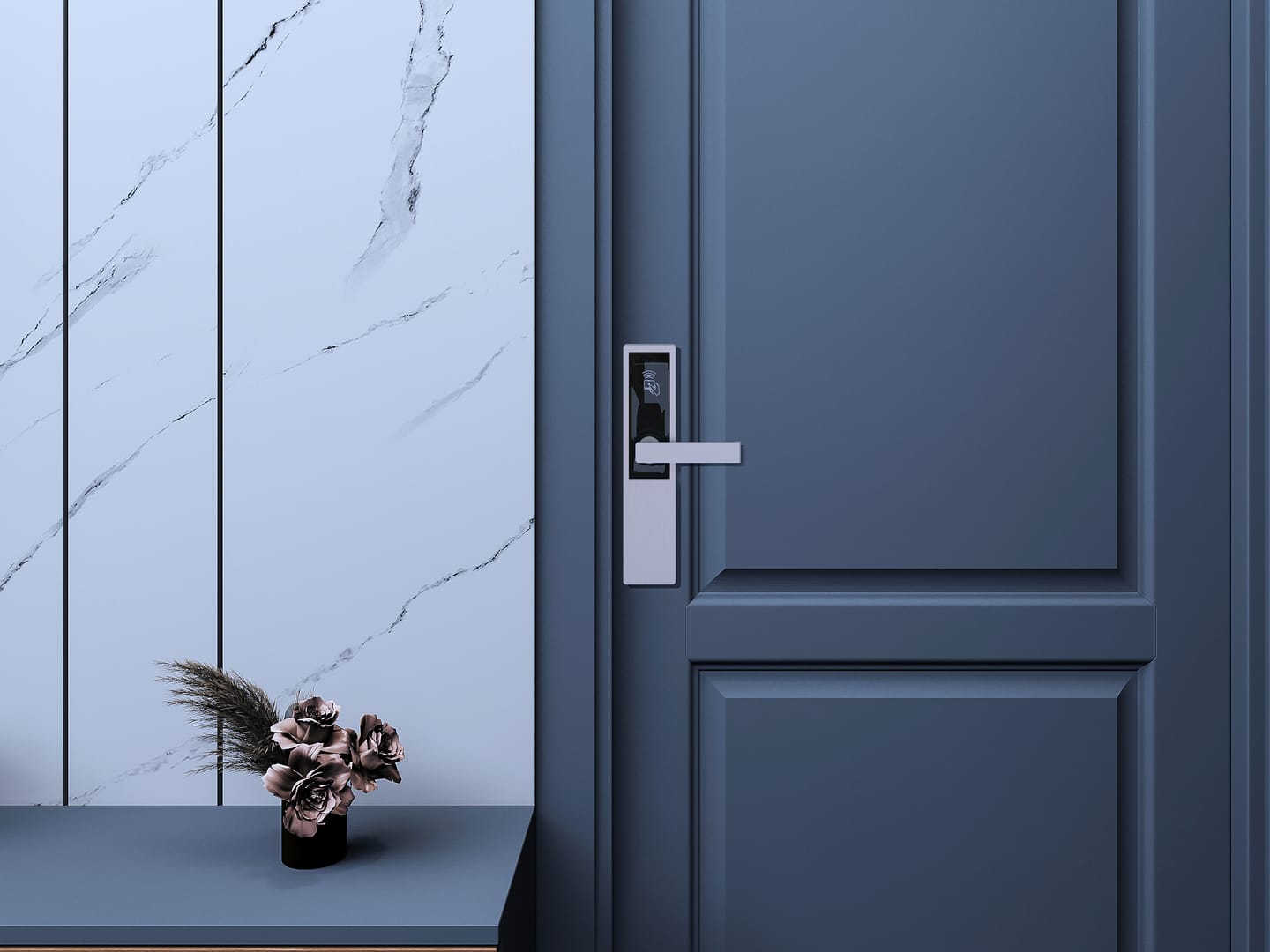
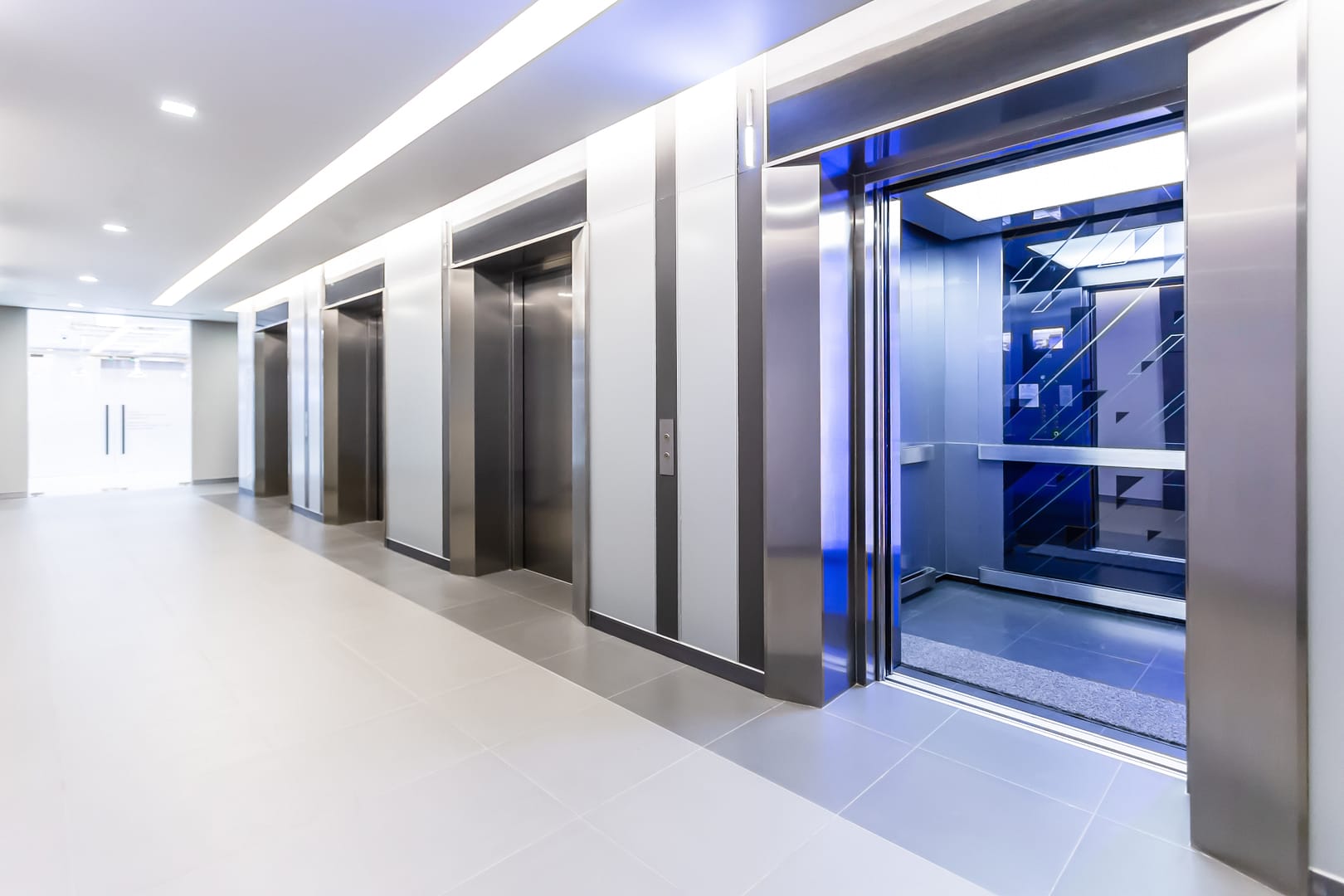
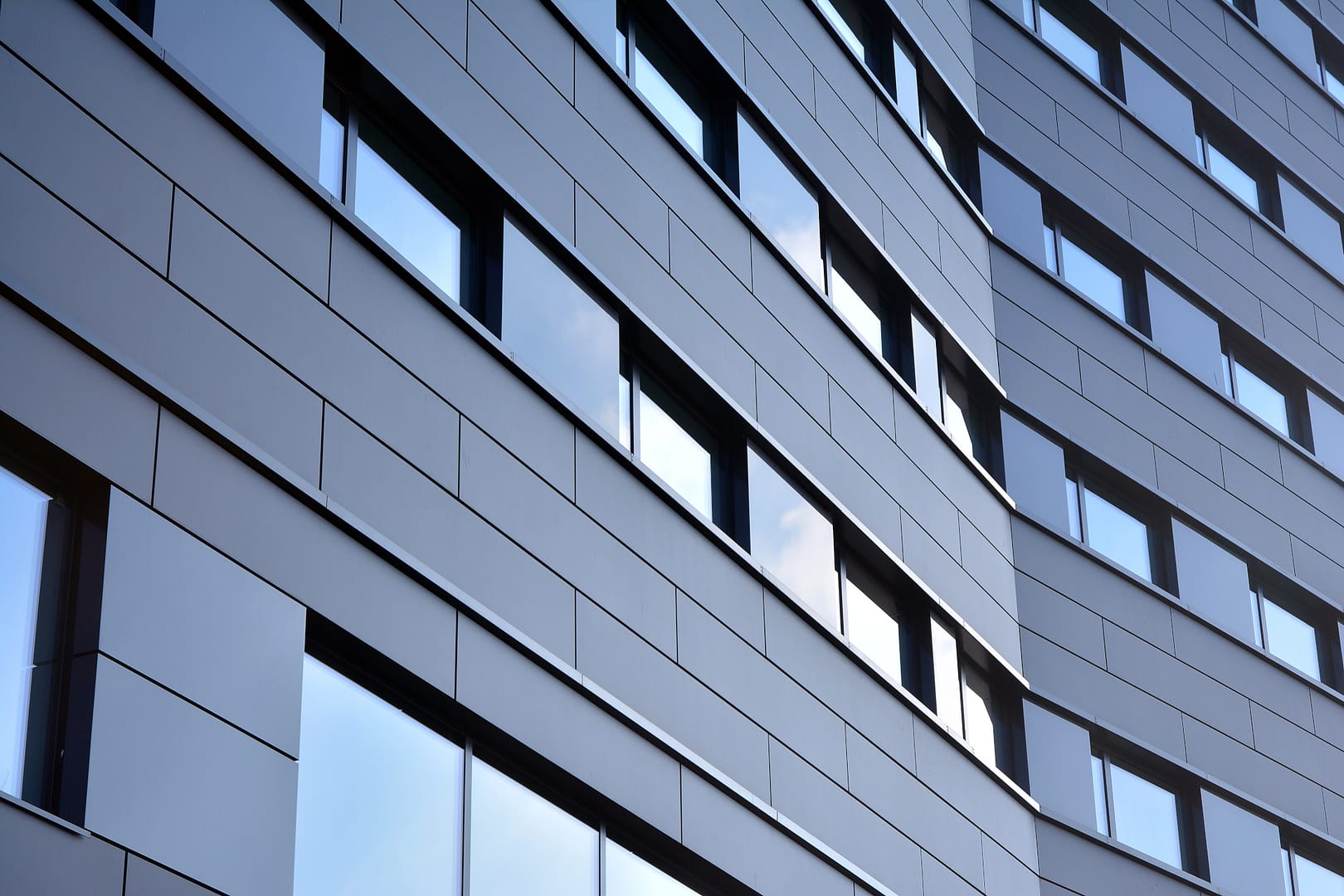
Panel-type products are widely used in both interior and exterior of buildings. The panels can be on either the floor, walls or the ceiling. Floor and wall panels are typically used in cold rooms and clean rooms, ceilings and acoustic panels are for office interior and marine cabins, and some pre-fabricated bathrooms and pre-fabricated housing are completely coated by panels.
CHALLENGES AND REQUIREMENTS (Façade Cladding)
For the higher-grade buildings the façade is defined by the architects, and the challenge arises to finish off with an impressive looking result. Each building is an individual and personalized. There are a lot of choices of standardized panels and there are some tailor-made options. Each of the manufacturers have their own requirements for their product designs.
The material used for façade cladding is typically mild steel, pre-painted steel or pre-coated steel that is sensitive and artistically patterned. Material thickness varies from 0.5 mm to 3.0 mm. For a single building the part order is usually a single production batch that has several different parts with variable dimensions. This requires a flexible production method; the same machine/line has to be capable of manufacturing straight panels, L-shaped panels and U-shaped panels. The parts also have to be manufactured in a correct order for delivery and installation. The series sizes are reasonably large and the total volume in the business is huge.
SOLUTION (Façade Cladding)
Pivatic offers automatic line solutions with punching, shearing and bending to meet the high-volume requirements. Traditionally the process to produce straight, L-shaped and U-shaped panels requires 4-5 different machines and buffer storages – with Pivatic all of the machine functionalities are in a single line process without buffers.
The flexibility requirements for different parts with variable dimensions are tackled with programmable punching centers, and the bending stations are equipped with automated hold-down tool changers. For interior panels that have a variable width, we use a cut-to-width shear to produce precise parts within millimeter differences. To match a straightness challenge with large panels Pivatic uses fine straighteners in the line solution.
To match the material thickness differences from 0.5 mm to 3.0 mm / 25 GA to 11 GA, Pivatic offers standard and heavy-duty machines for both punching and bending. The bending units are equipped with a crowning option. For sensitive materials, a PVC coating can be applied in the line to bolster the follow-up processes and installation, and all of the components in the line have a special coating to eliminate scratches to the parts.
CHALLENGES AND REQUIREMENTS (Ceiling Panels)
The ceiling panels usually have requirements for looks and for functionalities. The sheet metal panels are certified and rated for fire-resistance, and are mostly made from mild steel or aluminium. Acoustic panels are also widely used. With most of the interior ceilings the panels have to have an opening and closing function without damages, as they are used as service hatches for the tech inside the ceiling. The requirement for looks is highlighted in agencies, concert halls, airports and cruising ships that have artistically patterned ceilings.
SOLUTION (Ceiling Panels)
Pivatic offers automated flexible punching with press tool operations for both constant perforation and specified measure perforation. The variable corner notches are punched with Thick Turret tools as well as lighting and air flow openings.
The technology can be chosen for either coils or for blanks. With a coil punching line the perforated strip can also be recoiled for a follow-up blanking or a roll forming process.
The material challenges are met with special-coated components for sensitive materials, and the option to protect them with PVC coat in the line or beforehand. If aluminum is used for the perforated ceilings and they can’t be stacked via suction cups or magnets, the Pivatic stacking devices are equipped with special pliers or a dropdown stacker is used.
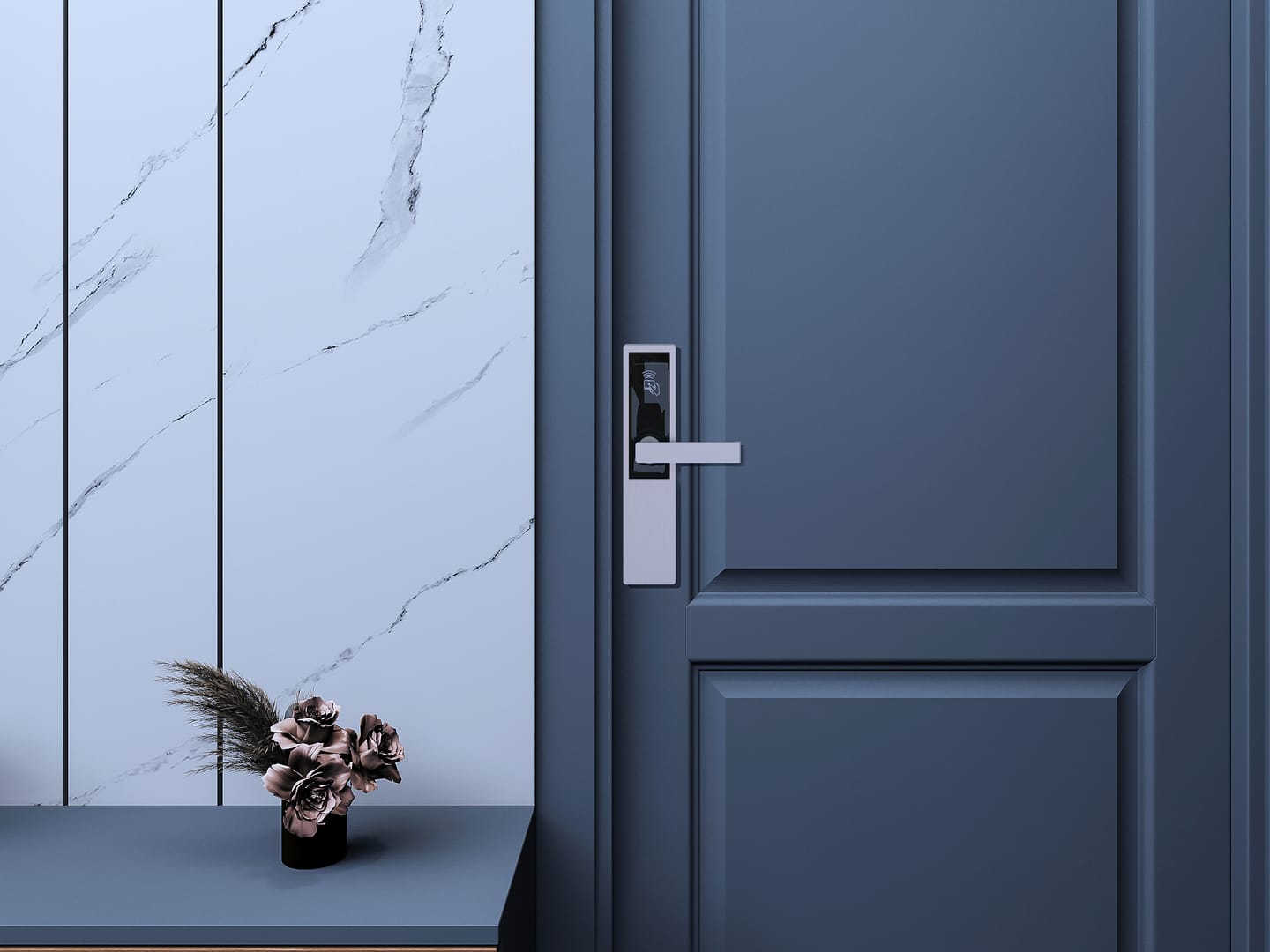
The market for steel doors in the construction industry is an ever-growing segment. With the growth in population and urbanization of areas, doors are an important part of building safety. Steel doors are overthrowing traditional wooden doors as they are cheaper to produce, lighter to install and more fire-resistant.
CHALLENGES AND REQUIREMENTS (Steel Doors)
A Steel door includes the cover plate and bottom plate with supportive parts and insulation material in-between. A steel door installation package also includes the frame parts. Steel doors are produced for two types of use; traditional safety doors or residential doors for households, hotels and schools – and fire doors for differentiating areas like an office and a factory hall, a garage and living area, or areas within cruise ships, airports, or hospitals.
Process
The manufacturing season for steel doors is when building construction is happening. On some areas, this is only half of a year when it’s warm. The doors have a high total volume, up to 500 doors a day, and a typical order can be a single hotel building. The production requirement to have both cover plate and bottom plate is 1 minute or under. Manufacturing the cover plate and bottom plate needs to be back-to-back since they are both required to finish a steel door product.
To assemble a steel door there are two methods that reach the required sturdiness. With the first method a polyurethane foam is extruded between the door cover and bottom plates and the door is compressed with a press. The polyurethane also works as an adhesive for the plates. The second method is adding insulative wool between the plates and to mechanically fasten the plates to each other. On top of the sturdiness that comes with intermediate material, it also improves the door’s resistance to fire and sound insulation.
Material
The types of steel door models are many. Fashion and modern designs affect the materials used to reach a certain look and feel. The high-volume door is cost-efficient and popular choice with a smooth surface, that can be used as an initial door which is changed later on to a higher quality door. A small number of businesses manufacture special doors in low volumes that have an expensive surface material or the door is compressed into shape.
The most common material used is 1 mm / 0.039” pre-painted or pre-coated mild steel, and up to 2 mm / 0.078” for the thicker fire doors. Exterior areas or sanitary facilities can have stainless steel doors. With the pre-painting or pre-coating of the mild steel customers can achieve different or individual looking designs, such as the wood effect coating. The cover plate and the bottom plate can be produced of different materials.
Steel door models
Punching
The challenges in steel door punching come from the size variables and hole changes from left-handed doors to right-handed doors. The holes for lock, hinges, handles, peepholes, and fixations all vary. When using a single line to produce both the cover plate and the bottom plate, the holes for lock and hinges change sides and the burr that happens from turret punching metal has be left inside of the cover and bottom plate. A question arises if the cover-bottom –combination should be produced upside –downside – upside, or to invest in mirrored or indexing special tooling. The standard hole features are required with parametric programming.
Bending
The challenges in steel door bending comes from the door size variables, cover-bottom kit production, and bending the thicker material fire doors. The profiles on each side of the door plates are standardized. As the punched door plate is fed into the bending, the burr side needs to be up. The size variables in cover-bottom kit production requires tool changes in the end benders’ part hold down. To bend the thicker material there are a limited amount of automated line suppliers and the manufacturers have to rely on press brakes that slows down the overall process. The special compressed doors or decorative extruded shapes needs to be noted in the material handling equipment and bending tool design.
For some of the thinner and simple design steel doors, the sides can be formed by a roll former and the ends can be upward bent in a separate machine or attached to the door profile as separate parts.
SOLUTION (Steel Doors)
A high total volume of steel doors requires an automatic process. With Pivatic systems you can punch and bend all smooth-surfaced and mildly decorative door models. The servo-electric machines are suitable for the thin residential steel doors and the hydraulic machines for the thicker and more demanding fire doors. A cover-bottom kit production can be run with one line fully automatically, and all the necessary setups between part size variations will be done without the need for an operator. The required cycle time of under 1 minute per a finished door, or in other words 500 doors a day, is achievable with Pivatics’ standardized solutions. There will be no wasted door plates when changing from one door size to another, as all variables are programmed, tested and finalized before customer delivery.
Pivatic solutions can manage mild steel from thin to thick in both punching and bending. Pre-painted or pre-coated materials are suitable for the production lines as all of the material handling equipment is designed for delicate materials. If the cover plate and the bottom plate are of different material, you can produce them from material-specific coils or blanks. This can be done by dedicated lines for each of the materials or with a single line.
The challenges in steel door punching are tackled with Pivatic coil punching and blank punching solutions. Both solutions utilize a flexible Thick Turret punching station that can be equipped with standard shape tooling, special tooling, or cluster tooling. With the left-handiness or right-handiness of the doors, several features such as holes for hinges will require mirrored punching patterns. This can be done with one indexing tool. To increase the production efficiency, you have an option to add an additional Thick Turret punching station with large tools or a HT Press Tool station. The door plates can be flipped over after the punching process to get the punching burr on the right side of the part.
For steel door bending, Pivatic’s bending lines are favored among several of the world’s largest steel door manufacturers. The concept for bending standardized profiles with different material thicknesses have been encountered and resolved for several decades in Pivatic. The bending lines can have the part flipping in the start if needed, and all of the size variations in a cover-bottom kit production are done automatically and parametrically in the process. Some decorative features, such as grooves, can be done in Pivatic bending lines before the side bends, and the grooves are taken into account in the bending units’ hold down tool design. To bend the thicker materials, Pivatic’s wing bending units can be replaced in the line with MPB benders designed for up to 4 mm / 0.157” material. If the door plates are able to be profiled, it is possible to integrate a Samesor roll former after Pivatic PivaPunch punching line.
CHALLENGES AND REQUIREMENTS (Steel Door Frames)
A single sheet metal door assembly requires two door leaves and four frame parts. Complete door assemblies are manufactured daily from hundreds up to a thousand, so the need for door frames are up to 4000 parts per day. This requires an efficient process and for mass production it is usually recommended to obtain separate manufacturing lines for door leaves and door frames.
Process and Material
Steel doors and steel door frames are used instead of wooden doors mostly in the USA and Asia due to humidity and fire protection requirements. The material used is similar to the elevator industry, so typically galvanized 1.0 – 2.0 mm mild steel with high yield strength (600 – 700 Nm) due to anti-corrosion. The bottom frame can be stainless steel to withstand collisions better. A small amount of the frames produced are from pre-painted or pre-coated material, similar to the door leaves. The frame parts are parametric and the lengths vary by the door height and width dimensions, from 150 to 3000 mm. The frame width depends on the thermal insulation requirement installed within (wall thickness) and the type of the profile, from 170 to 500 mm.
Punching
The challenges for punching come from narrowness of the long parts, that leads to high accuracy and straightness tolerances. To attach the top frame to the sides there are several punched holes on both ends. The parametric hole patterns and a form embossing for the lock mating plate require special tooling. The cycle time requirement for a single frame part is 15 – 25 seconds to match the general production time requirement of 45 – 60 seconds for a steel door assembly without the bottom frame.
Bending
The challenges for bending comes from accuracy requirements to fit a robotized assembly and welding, the small dimensions between bends, and special shapes to increase sturdiness and fire protection rating. One production line or machine needs to be able to produce all of the commonly used 5 – 7 different profile shapes, where the width varies according to the wall thickness.
The side frame and top frame profiles are identical and determined by the door leaf profile. The bottom frame can be of similar shape or a shape of its own.
Example frame profile shapes
SOLUTION (Steel Door Frames)
Pivatic offers complete solutions of door frames in high volumes as series or as kits. The punching and bending machines are available as electric or hydraulic, depending on the material thickness that’s used. For the parametric part production, we offer nesting machines for both coils and sheets. If the production is in large series, we recommend using a production line for wide coils and to nest the frame parts side-by-side. If there is a large material variance, we recommend using a production line starting from a high sheet tower storage with similar side-by-side nesting.
To fill the high accuracy and straightness requirements in punching, we cut all of the frame parts on all four sides with shears regardless of whether the process is started from coils or from sheets. The raw material is fed to a TT punching station with several feeding clamps to ensure that the material is staying straight. By nesting the frame parts on wide coils or sheets, you get the full benefit of double tool punching the side-by-side frames simultaneously. To increase efficiency on hole patterns or to produce the forms on the lock mating plate, you can add an additional Thick Turret punching station equipped with cluster or shape.
To bend different door frame profiles, we offer solutions for all types of frames. Our own bending machines are suitable for the sealed frames that are difficult to roll form, and in bending the thicker sealed frames a robotized press brake can be included. The simplest profiles can be produced by integrating a roll forming device after the PivaPunch punching line. The lock mating plate form is always evaded by automatically aligned hold down tools of the benders.
Special equipment to finish up the process can be included in our modular line solutions. These can be for example adding a protective film on the material before punching, to mark the frame parts by laser to add traceablity, to have robotized welding, or even a complete robotized door assembly.
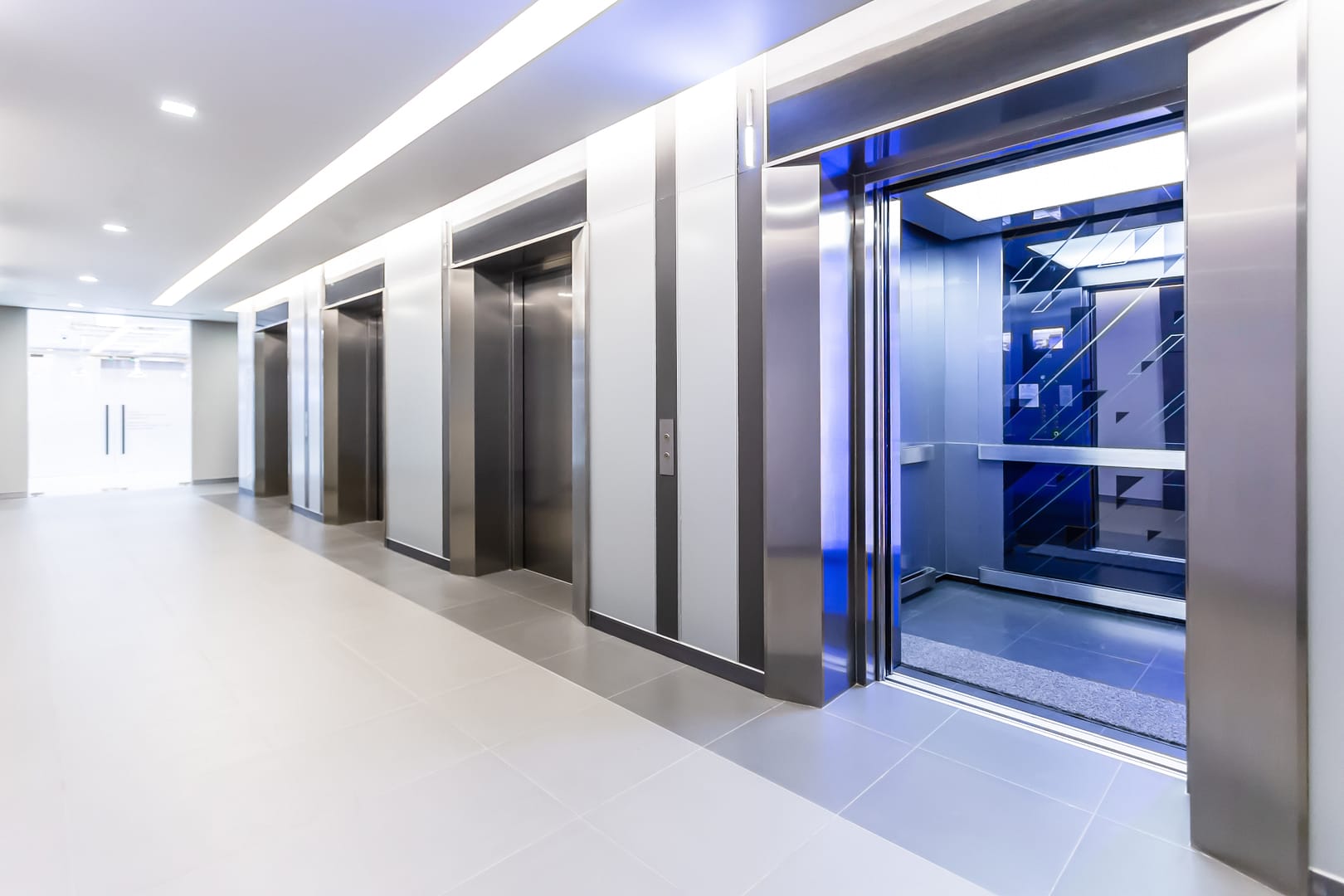
Elevators and escalators are a part of the construction industry which is always blooming. Parts are produced in the millions every year. The elevator cars have their frame interior, walls, ceiling panels, control panels, and car doors all produced from sheet metal. Every floor has a set of landing doors. Pivatic focuses on the production of car panels as well as both landing and car doors.
CHALLENGES AND REQUIREMENTS (ELEVATOR DOORS)
A single elevator car includes 2 single-leaf or 4 composite doors (also referred as a gate). And every floor by the elevator shaft has 2-4 landing doors. A typical office building consists of 2-4 elevator car doors and around 30 elevator landing doors.
The elevator car manufacturers are often also producing the elevator car doors, but the elevator landing doors have their own manufacturing companies. Both door types have two types of end-products: single-plate doors and cladding doors. A cladding door is a mild steel plate that is coated by a glued thin stainless steel exterior for aesthetics.
Single-leaf and composite door assembly
Single-plate door and cladding door
For the manufacturers, a single production batch is typically the required amount of elevator doors for one building. Apart from office buildings an order might also be a box of flats or other high-rise building. The door size is often standardized for bulk doors and customized for the decorated ones. A demand for tight tolerances prevails for the whole industry to ensure consistent quality for mass production.
Production batch size examples
Process and Material
The bulk door is made from mild steel for standard doors or stainless steel for fire doors. Manufacturing companies that produce decorated doors tend to use SUS304 magnetic stainless steel instead of standard stainless steel since the corrosion resistance is not required indoors and the material softer and easier to shape. The decorations can be ordered completely by the end customer, so it is common for the production process to start from a blank storage system with several different types of coatings.
Punching and Bending
Challenges for the punching are not many, but the punched blank is always required to have cut-free edges. The cut-free can be made by grinding, rolling or hemming the edges. Challenges for the bending are strictly about the tight tolerance requirement and the straightness for the end-bends, as the door is hanging on a hinge from above. The material springback needs to be tested and corrected properly for all of the used materials.
Once the elevator door is bent complete, it will often have to be finished by spot welding to ensure stiffness. For pre-coated or pre-painted materials, a TOX-clinching or other material-friendly stiffening methods needs to be used in place of welding.
SOLUTION (ELEVATOR DOORS)
The enormous production volume of the construction industry requires an automated manufacturing solution. With Pivatic systems you can punch, bend and finish the end-products with superior cycle times and part quality.
Pivatic punching and bending lines can process mild steel, stainless steel and pre-coated steel according the industry needs. To ensure that decorative materials stay unharmed, all line components are designed as scratch-free from punching to bending. Applying protective film or pre-coating can be done in the line if required.
For high material variance production, Pivatic blank manufacturing solutions are the correct choice. The blanks are automatically unloaded, punched complete and stacked or forwarded from the process. It is possible to use pre-cut blanks that are only cut-to-length, but ideally it is recommended to produce a cut-to-size blank from coil in the Pivatic process. This way the high tolerance requirement is always met by the material standards, leading to fewer problems in optimizing the bending process.
For low material variance production, Pivatic offers both blank manufacturing and coil manufacturing solutions. With standardized dimension changes and custom-sized doors the recommendation is coil manufacturing from one wide coil. By having a single wide coil for all of the required materials, and by shearing to size of the doors, the needed material storage size decreases significantly in addition to less logistics costs.
To meet the challenges for punching, all standard holes and hole patterns can be punched with flexible Thick Turret punching station. The cut-free edges for the parts are achieved by edge forming rolls that are integrated into the feeding device for the punching station. If Pivatic is only the supplier for the bending solution and the punched blank edges aren’t grinded, rolled or hemmed, they can be done with an additional device before the first bending station.
To meet the challenges for bending, Pivatic specializes in high volume automated production. A standard cycle time is 20 seconds per door to offer uniform quality production. The variations in door sizes are handled by automated hold-down tool changers. For a high material variance or exceptionally high or thick elevator doors, Pivatic offers the heavy duty MPB Multitool Bender in place of the traditional wing benders. The MPB is capable of bending up to 3 mm / 8 GA thick steel and up to 3 000 mm / 118” part length. The required straightness for end-bends is guaranteed by a promise of ±0.15° bending angle tolerance.
To finish up the product Pivatic bending lines can be integrated with spot welding station or a TOX clinching press.
CHALLENGES AND REQUIREMENTS (ELEVATOR CARS)
The elevator car manufacturers are different from the elevator door manufacturers, but might have the car doors in production in addition to the car panels. The most common elevator car panel to produce are the wall panels: a single elevator car consists of approximately 10 panels. Panel sizes used are standard in width, but the car size determines the width of required corner panels that are used to compensate car size variations. The series sizes are small but total production volume high, just as for the doors: a single order is a single building.
Elevator cars are commonly in standardized sizes, but the decorated models have customized sizes. The car height varies by European, Chinese or American standards of 2100, 2200 or 3000mm (82”, 86” or 118”), with the focus globally on the higher models. The higher the elevator car is, the longer and thicker the panel is required to be for appropriate stiffness.
Material
The materials used in manufacturing are commonly standardized with little variations. High tolerance requirements for the parts are potentially due to door manufacturing tolerances, even though they have no function for car panels. For the required thicker material of the highest elevator cars, the cut-free edges provide more difficulties to solve. The standard materials have a lot of different coatings and decorations in place that require a scratch-free process.
Punching and Bending
The challenges in steel door punching are tackled with Pivatic coil punching and blank punching solutions. Both solutions utilize a flexible Thick Turret punching station that can be equipped with standard shape tooling, special tooling, or cluster tooling. With the left-handiness or right-handiness of the doors, several features such as holes for hinges will require mirrored punching patterns. This can be done with one indexing tool. To increase the production efficiency, you have an option to include an LT Large Tool station or a HT Press Tool station after the flexible Thick Turret station. The door plates can be flipped over after the punching process to get the punching burr on the right side of the part.
The difficulties for punching or bending are a few, but the long blank and thick material may be problematic. Most manufacturers only require a few holes for panel attachment to the frame and single 90° bend per side. A rare occurrence of Z-bends can be within the car panel sides.
SOLUTION (ELEVATOR CARS)
High total volume for the industry is optimal for Pivatic. The automated line solutions it is possible to produce different sized car panels seamlessly back-to-back. The recommendation to produce panels outside of standard widths as their own kit within the production order for the best cycle times and material savings. As their own kit also the setup times for the bending line is minimal.
For production with small material variance, it is optimal to use one wide coil for the manufacturing, that can be used to create multiple days’ worth of the dimensioned cut-to-size blanks and punching them complete. The cut-to-size before punching meets the high tolerance requirements better than traditionally produced blanks. A kit of different-width blanks can also be cut-to-size before punching, where the panel height (e.g., part length) is identical to the parts inside a kit for zero material loss. Pre-cut blanks can be used in Pivatic punching lines but they are required to have a proper edge straightness. To create cut-free edges for all parts Pivatic uses edge forming rolls in the feeding device for the punching station.
All line modules of Pivatic are material-friendly and designed to be scratch-free. The lines are suitable for pre-coated and pre-painted materials, and it is possible to add protective film on the material to reduce any complications to the material in packaging or delivery.
To produce the highest of elevator car panels of thicker materials Pivatic offers heavy-duty bending lines or the option to integrate certain Panel Benders. The small series sizes and the rarely needed Z-bend are possible with either of solution types.
To get tailored solution to fill your manufacturing needs, please contact our technical sales team.