Schneider Electric is a global company specialist in Energy Management and Digital Automation head-quartered in France. At its production site in Capellades near Barcelona in Spain, Schneider Electric manufactures electrical cabinets and distribution enclosures on highly automated equipment. A poster hanging in front of a combined punching and bending line already proves that automation is worth it. This sheet metal processing line integrates punching modules from Pivatic and a panel bender from RAS. Schneider Electric figures the increase in efficiency due to this line at 410%.
But step by step. Schneider Electric over the years has constantly evolved its punching and bending processes of sheet metal parts. Bending of sheet metal components began traditionally on manually operated press brakes.
There, the completion of a single bent part took 20 minutes. In the next step, Schneider Electric upgraded to press brakes with robotic automation. At that time, the blanks came from stand-alone punching machines. This was already a big step forward and reduced the production time to 4 minutes per part. Today, the Spanish company produces the top covers and wall panels of the electrical cabinets, as well as the mounting plates, on a Pivatic-RAS line. Every 49 seconds, an unloading robot removes a mounting plate at the exit of the production line and stacks it. For less complex parts, the cycle times are even shorter.
The production line starts with a Pivatic punching machine. A loading module feeds the sheared blanks to the system, which are stacked on two pallets.
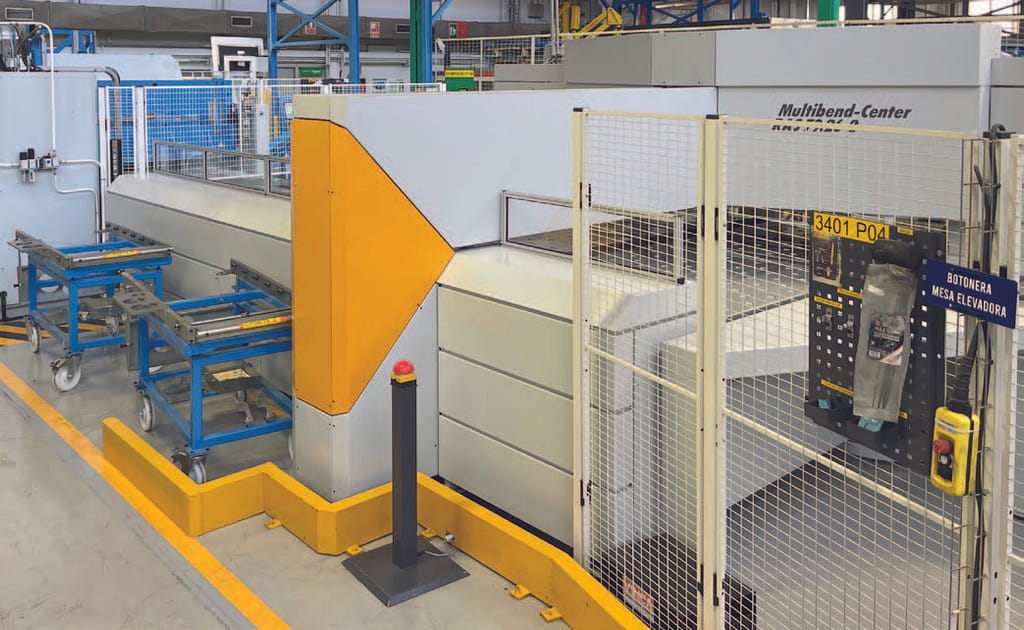
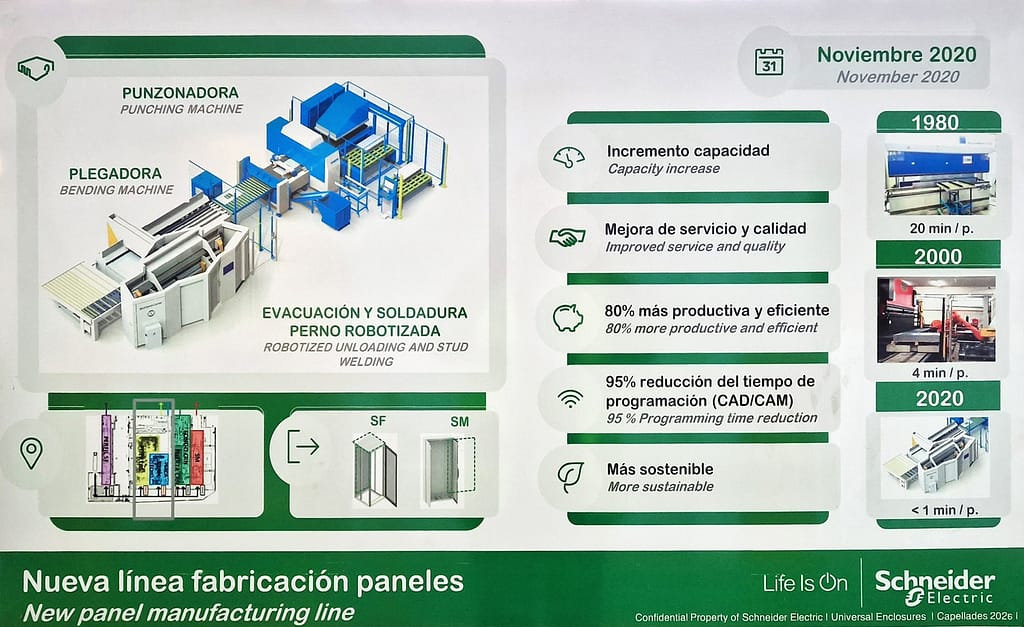
When the destacker picks up the blank from the pallet it also verifies the thickness and length of the blank. If the material measurement doesn’t match with programmed tolerances the destacker returns the blank and sets up the alarm for the operator to proceed recheck of blank dimensions or change the blank code or dimensions in production order. Originally, Schneider Electric had considered working from coil, but the space required for such a system was simply not available on the shop floor. Since Pivatic‘s lines can start with coil material as well as with blanks, the company opted for the blank version due to space limitations. A forklift loads the line with cut-to-size packages of blanks on which either 20 or 32 sheets of 1.5 mm or 2.5 mm galvanized steel are stacked. These batch sizes match the subsequent working operations in the assembly area.
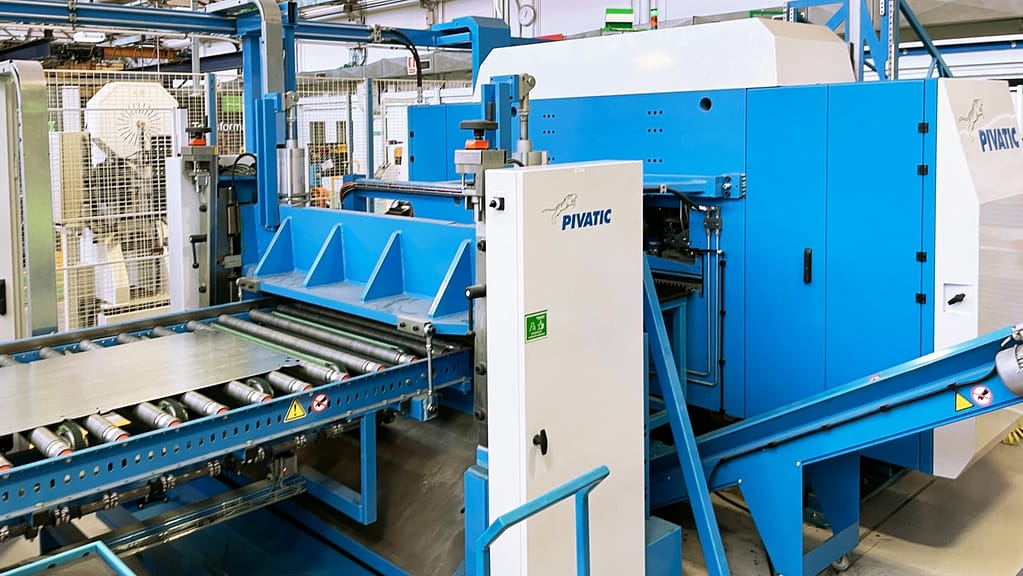
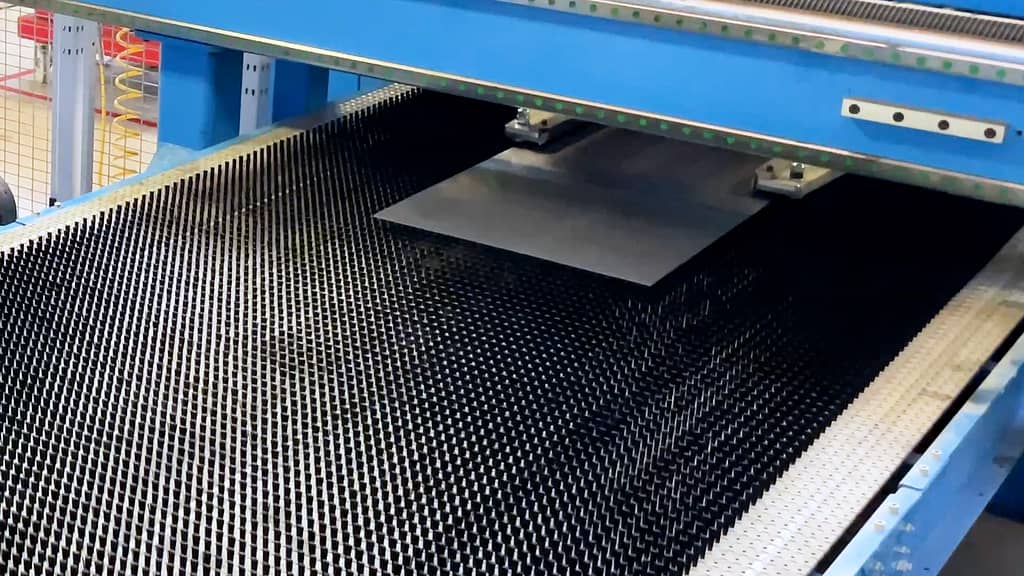
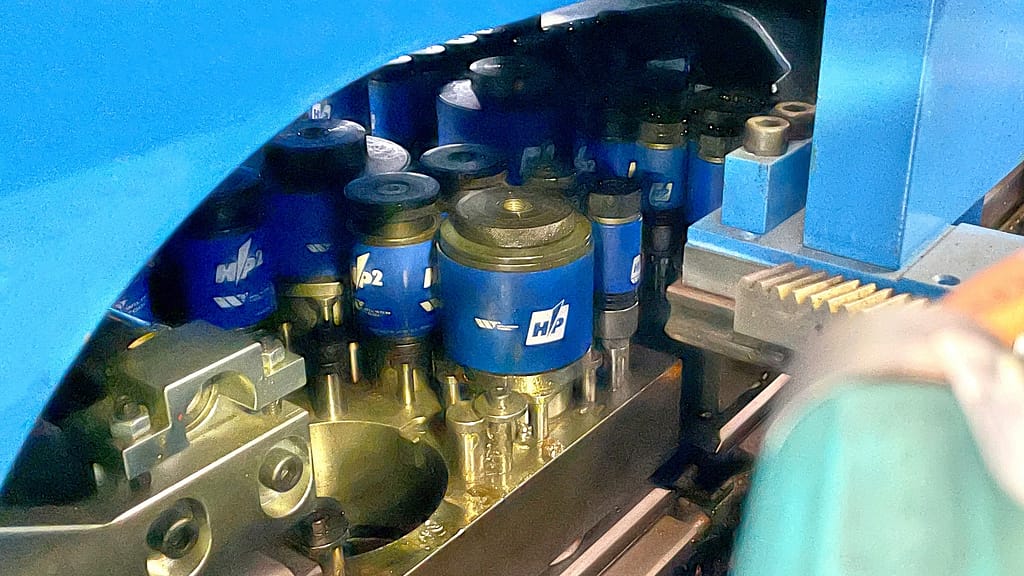
During ongoing operation, a stack of material for the subsequent job can already be loaded. Schneider Electric needs this flexibility in order to meet market demands. Due to the small batch sizes, the parts inventory of semi-finished products can be kept at a minimum.
Side pushers align the incoming sheets to be centered in front of the die punching system. At the same time, the servo feeders give feedback on the measured blank width, and if any variation is noted the blank will be rejected. A manipulator in front of the die punching machine moves the blank forward and positions it. The blank runs through the punching module only once and stops at each punching position. The punching system is equipped with two C-frames in which the punching tools are inserted. They move in and out at right angles to the flow of the blank and can reach any position on the blank. On top of tools and selector, there is a servo-electric ram getting its 300 kN stroke force from a linear servo motor. This flexible operation results in an extremely high punching speed. Faster than any other flexible punching process. This is also necessary in order to keep up with the speed of the downstream panel bender and to avoid bending downtimes.
Behind the punching module, a second feeding manipulator takes over the punched blank. If needed, a downstream cut-to-length shear can separate the blanks in the middle. In the next step, the punched blanks are transported via a roller conveyor to the RAS panel bender. A lateral pusher aligns the punched part to a reference line before infeed grippers pull the sheet onto the measuring table of the panel bender. There, a laser measures the position of the blank and transfers the data to the main manipulator.
This manipulator positions the part with an accuracy of a hundredth of a millimeter and rotates it with a precision of 1/1000 of a degree. With the program start, the grippers of the tool changer setup the individual upper beam tool segments exactly to their specified position. Once the part has arrived on the bending line, the upper beam tool clamps the sheet against the lower beam. The folding beam then bends the workpiece up or down in accordance with the programmed sequence.
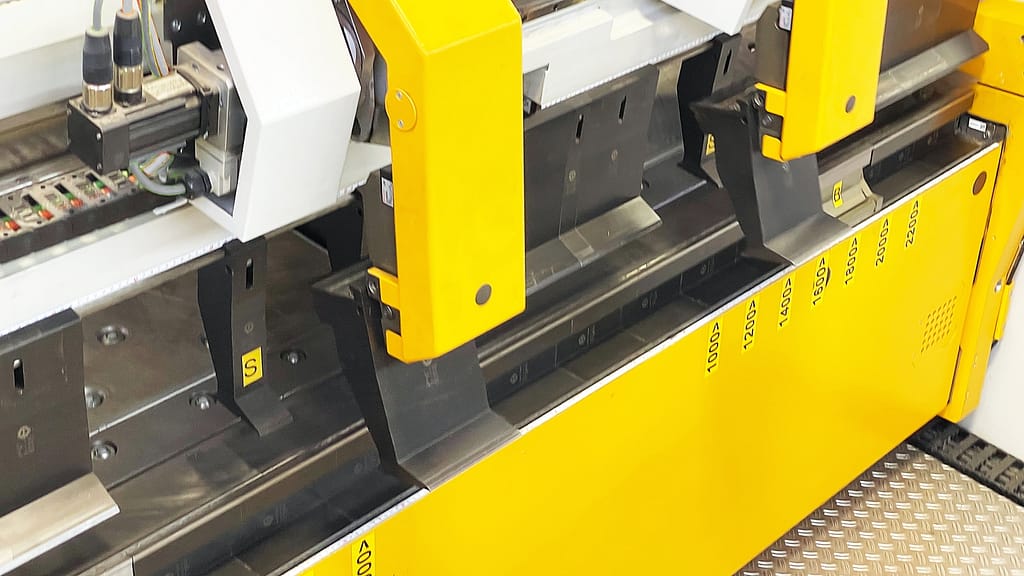
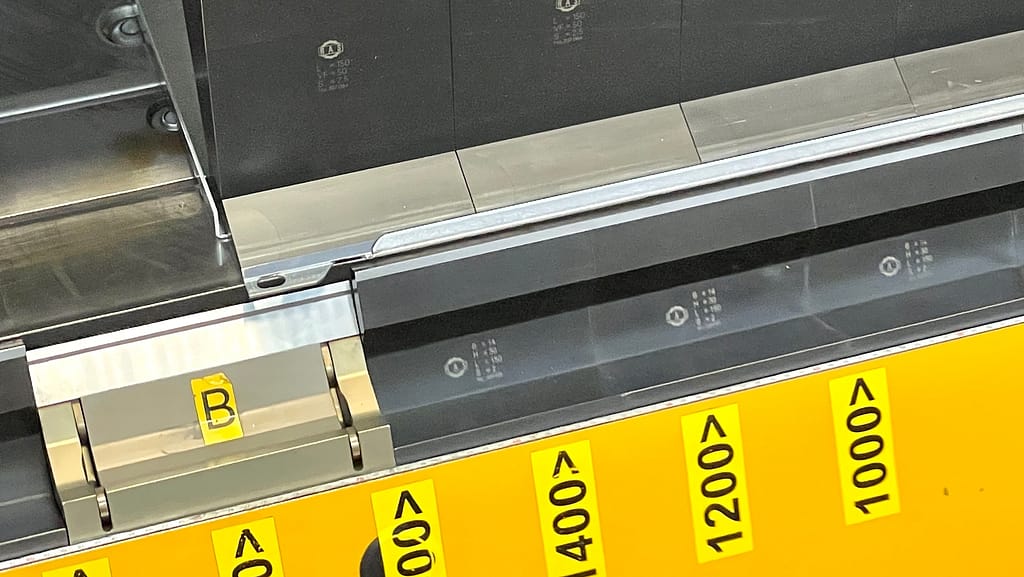
After all sides of the blank have been bent, the main manipulator pulls the part back. While the run-out conveyor belts move the finished workpiece out of the bending cell, the main manipulator starts to the next blank ready to be bent. This means that it only takes about 4 seconds until the bending process starts on the next part. At the end of the run-out conveyor, the finished part is aligned once again. From this position, a robot takes it over and positions the bent part in a stud welding station, which completes the bending panel with a grounding stud. Next, the wall elements or upper parts are transferred to an outfeed station with a tilting device. The operator picks up the rotated components from there and places them vertically in transport racks. The robot on the other hand palletizes the assembly plates in a horizontal position. The vertical or horizontal alignment is matched to the downstream processes in powder coating or assembly.
Manuf. Engineering & Maintenance Manager describes some of the advantages of this complete punching and bending line: „Speed and flexibility of the system are very important for us. Small quantities produced quickly result in low unit costs.“ The system produces 350 bent parts per shift. This number is adapted to the downstream production steps, but could also be increased to 600 parts. Joan Tarrida, who is responsible for the manufacturing methods and automation adds: „It is becoming increasingly difficult to find skilled operators. Therefore, we decided to use automation at an early date. Today‘s system requires only a single operator and this operator does not affect the speed or precision of the punched and bent parts.“ At the same time, the accuracy of the production parts is so high that at most, the first part of a batch will be checked. After that, Schneider Electric‘s manufacturing specialists can rely on the repeatability of the system.
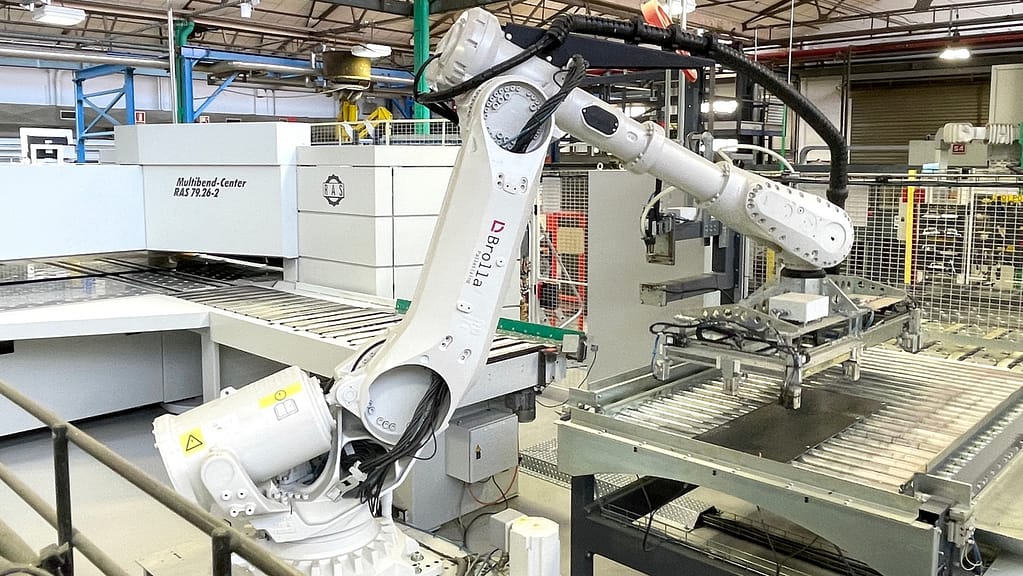
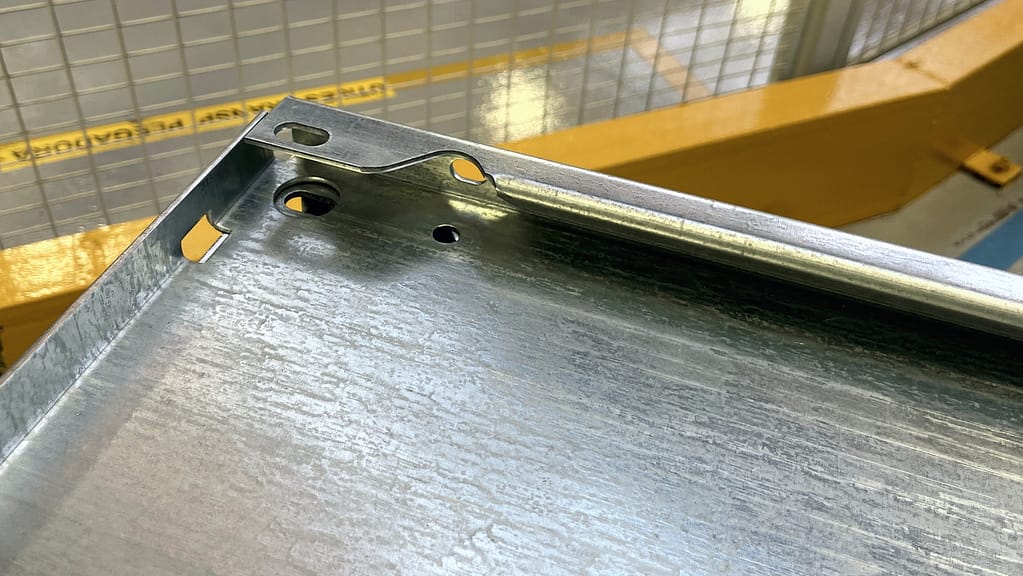
Some of the bent parts do have special characteristics. For example, the mounting plates are bent from 2.5 mm galvanized steel. Since they will not be powder-coated at a later stage, they must be visually flawless and must be free of scratches on the bending lines. Some punched holes are also located near the bending line and may not deform during bending. The RAS panel bender can meet all these requirements as the folding beam tool forms the material using its entire surface.
The punching machine applies several embossings to the blank for the top cover. They are located close to the bending lines. This requires cutouts in the foot of the upper beam tools so that the embossings are not flattened during clamping. However, in order not to weaken the entire upper beam tools by these cutouts, RAS uses only individual milled-out tool segments. The tool changer positions these special tools and even repositions them during the bending sequence. In the bending process, the folding machine forms only a slight chamfer on all four sides of the top cover. Schneider Electric tested this requirement with several suppliers and only found a high-quality solution with RAS.
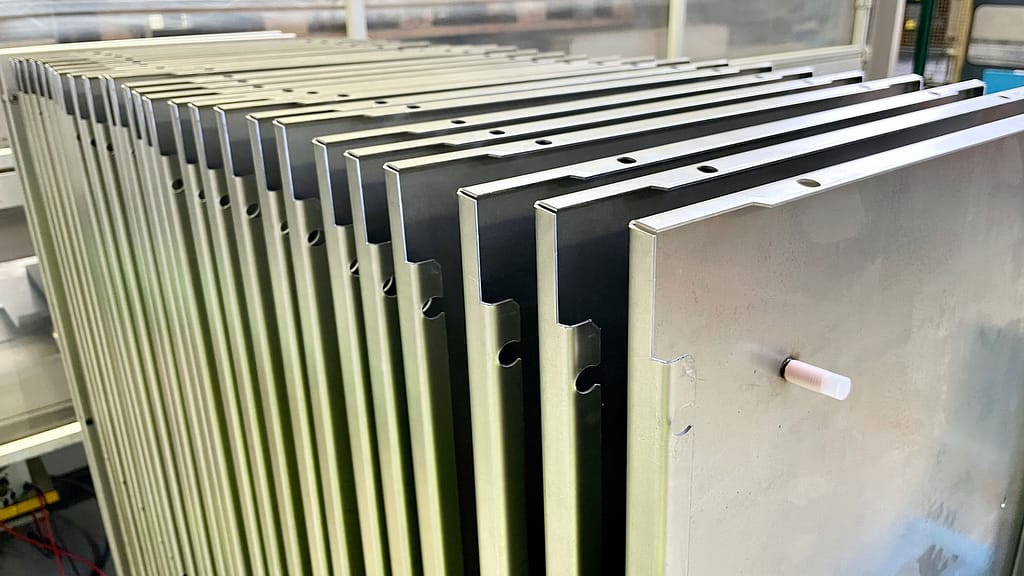
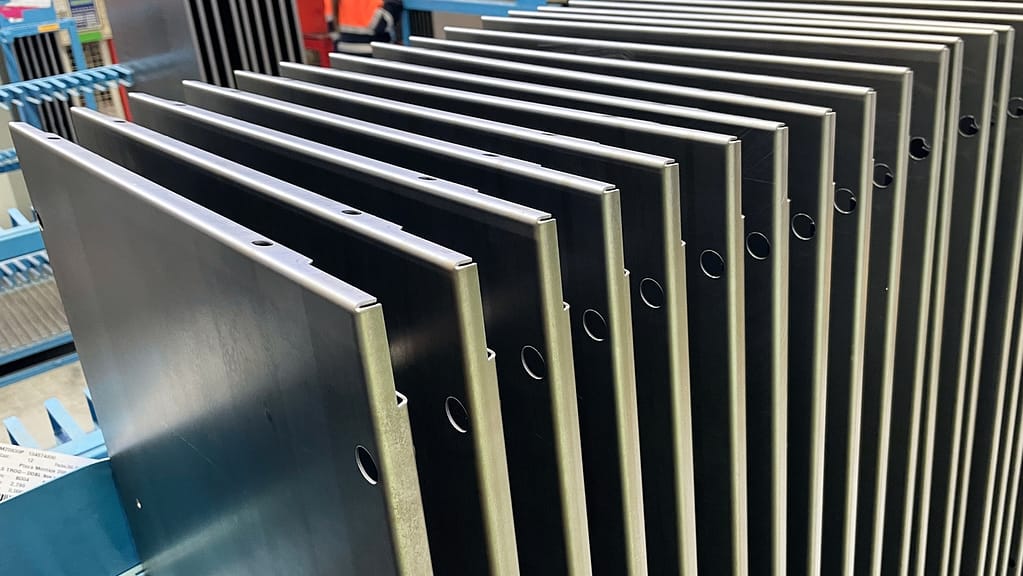
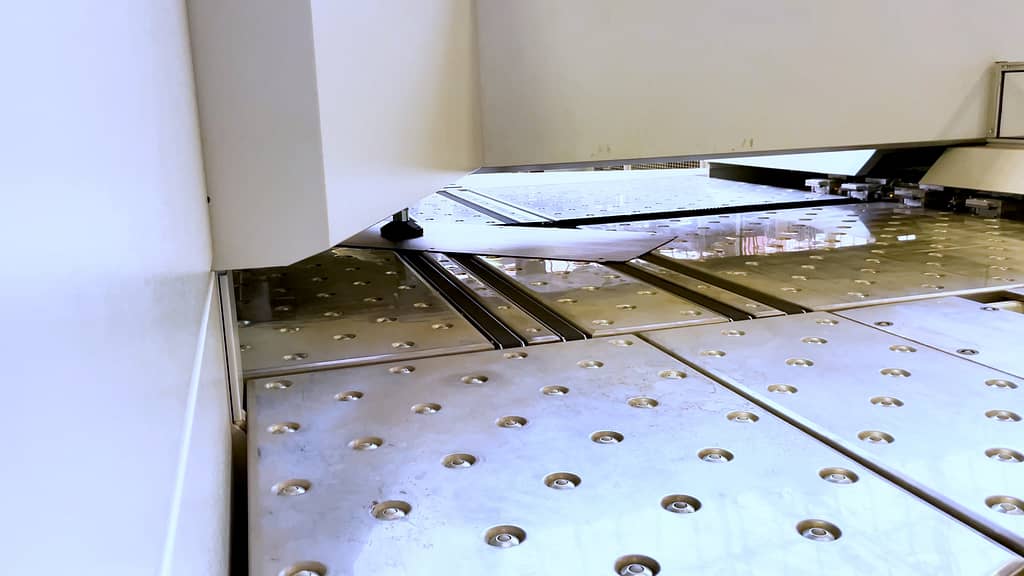
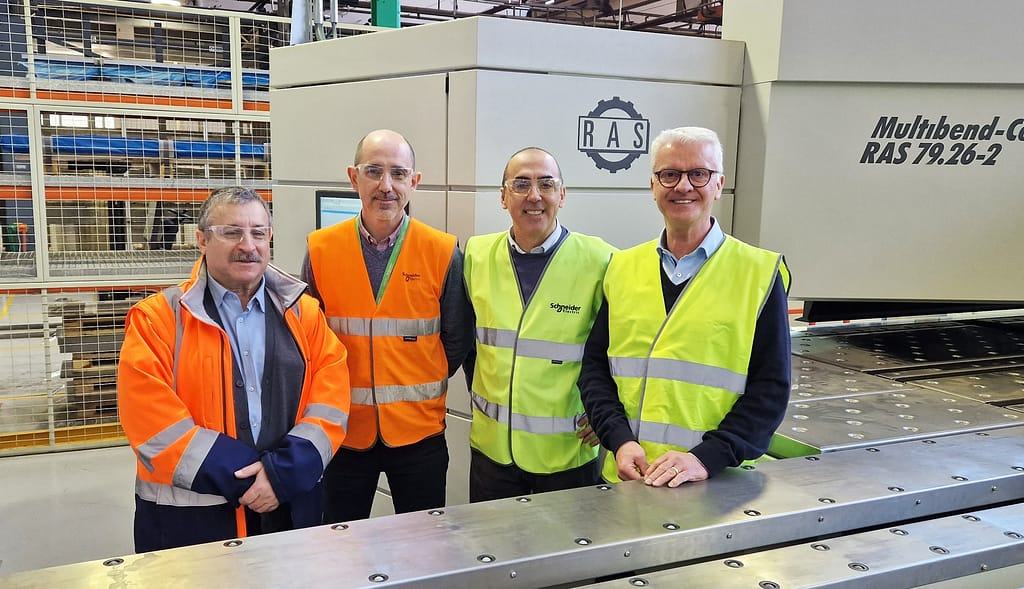
The panel bender has also established stable conditions in terms of angle accuracy and repeatability. When bending on the press brake, zinc abrasion always built up on the die edges, combined with scratch marks on the bending lines. Using the folding technology today, the parts are visually flawless, and cleaning of the tools is no longer necessary. Due to the zinc buildup, the bending angles also constantly changed and so the machine operators had to adjust the press brake programs again and again. The metal folding technology from RAS has eliminated all these headaches.
Ramon Alfonso and Joan Tarrida agree: „The Pivatic- RAS line for punching and bending our electrical cabinet panels has created a huge productivity boost. Compared to the automated press brake bending we have become at least 50% faster in set-up and 25-50% faster in bending.“ Ramon Alfonso concludes: „Currently, we are running the line in one and a half shifts. We are planning to bring currently outsourced electrical cabinet components back inhouse and thereby gain further cost advantages.“
© RAS Reinhardt Maschinenbau GmbH