Meet us at EuroBLECH 2022 – Stand E136, Hall 11!
We will be showcasing a fully automated servo-electric coil punching, cutting and pressing line on the stand. Highly efficient and indexable Thick Turret punching combined with a separate cutting station and a press tool station of 1200 kN punching force allows jobs like hole group, embossing, corner notching and trimming to be flexibly produced. Energy consumption for the full line is between 12-18 kWh, depending on the use of the big press, which is 60-70% less compared to traditional systems. This supports Pivatic’s low-energy product solutions well toward global sustainable development.
The line is bought by a German manufacturer who will receive the line after the exhibition with two coil cars, a turning drum, and a stacking device that are not present at EuroBLECH. The line is made in custom blue line color.
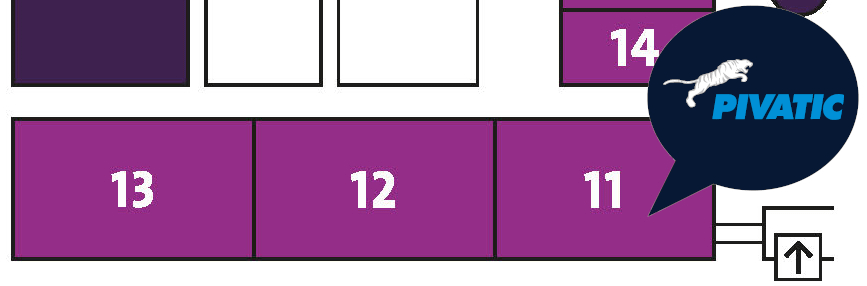

The electric PCC-e punching centers utilize servo technology which allows significant energy savings. Both force and stroke of a plate ram, driven by a linear motor, can be CNC controlled now. That allows very fast punching with less energy consumption. With very precise control, forming is considerably faster and more precise than ever before. Our punching lines can also reclaim the braking energy of the servo motors in punching stations and presses and reuse it in the process. In addition to energy savings, our modern lines will reduce your service costs, requires less floor space, and have a lower overall noise level.
Pivatic Worldwide
We have been operating for nearly 50 years. As of today, our sales and service network cover over 30 countries to provide local support for new machine sales and to ensure continuous high performance of the installed production lines. Find out who’s your closest Pivatic Sales Partner on the Contacts-page.
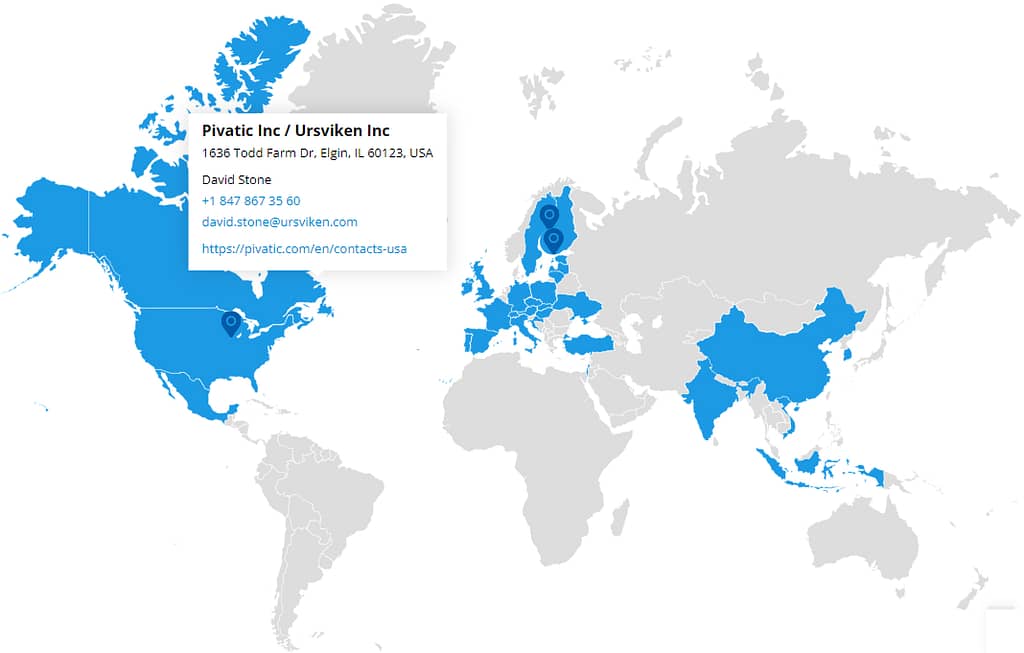